COMPENSATION MANAGEMENT: WAGE PAYMENT SYSTEMS
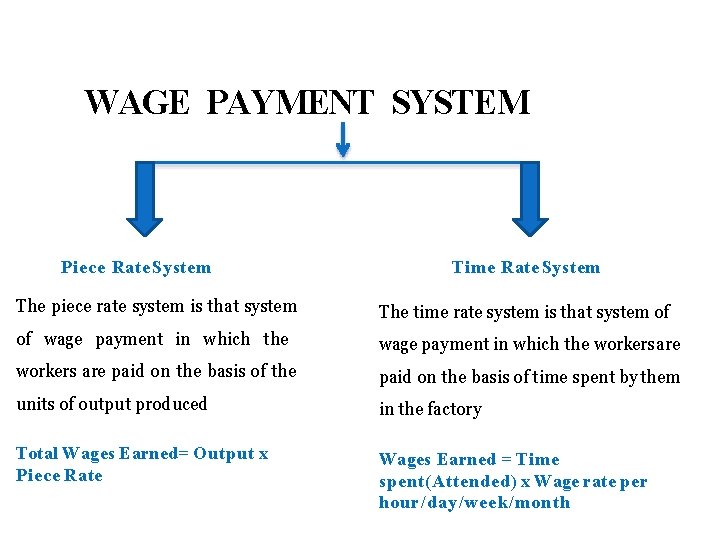
TIME RATE OR TIME WAGE SYSTEM
Time Rate or Time Wage System is the most popular method of wage payment. Known by various other names such as time work, day work, day wages and day rate, the payment is made on the basis of attendance. Wages are paid to the workers on time basis irrespective of the quantum of production, at a specified wage rate. The wage rate may be fixed on hourly, daily, weekly, fortnightly, or monthly basis. Calculation of wages under this1 method of wage payment takes into account:
- the time spent by the worker and,
- the wage rate per unit of time fixed. The formula is:
Wages = Time spent x Wage rate per unit of time
For example, if a worker gets $ 10 per hour, he works for 8 hours per day and has been present for duty on 25 days during the month, his wages for the month on the basis of time rate system will be:
(25 x 8) hours x $ 10 = $ 2,000
Thus the worker is paid on the basis of time and not on his performance or quantity of output.
Suitability of Time Rate System
The system may prove to be quite ideal is the following cases:
- Where quality of production is relatively more important than quantity, e.g., tool room, testing and inspection, etc.
- Where it is difficult to measure the performance precisely, e.g., the performance of indirect workers, night watchman, gate-keepers, maintenance and repair work, etc.
- Where output of the worker is beyond his control, e.g., where his speed of work is restricted by the speed of machines or conveyor belts, or where his work is dependent upon the work done by other workers.
- Where close supervision of work is possible.
- Where the nature of work is such that there is no basis for incentive plan, e.g., night watchman.
- Where production is intermittent on account of delays, power shut-down, etc.
Advantages
Important advantages of this system are the following:
- Simplicity – It is simple to understand and operate.
- Economy – The system is economical. Records of labour are simple and less detailed. This means a saving in overheads.
- Quality output – The system results in better quality of output aim workmanship since workers are in no hurry to complete the jobs.
- Offers fixed minimum wage – The system offers a fixed minimum waggle the workers for a defined period of time. They are assured of s earnings in spite of work stoppages or due to below par efficiency cans by personal factors.
- Elimination of speeding – Speeding is eliminated as the security of minimum wage is ensured to the workers. Speeding would have result in poor health of the workers and wastage of raw materials.
- Equality and unity among workers – The system is generally preferred trade unions because uniform rate of wage is given to workers irrespective of efficiency. It maintains unity among workers.
Disadvantages
Although the time rate system is a common system of wage payment and widely applied, yet it has the following disadvantages:
- Unfair – As the wages are paid on the basis of time irrespective efficiency of the workers, there is no correlation between the outputs an wage of a worker. The more efficient worker gets no extra reward lord his efficiency. The wages of a beginner and an innovative and experience worker may be the same.
- Discontent and Turnover – The system may cause discontentment among the efficient workers and they may leave the organization resulting labor turnover.
- Reduction of efficiency – Efficient workers may become inefficient because they notice that the inefficient workers also get the same wages.
- Increased cost of production – The cost of production per unit is higher; there are direct incentives to workers to work slowly which ultimately results in doing the incomplete work during overtime and overtime wages are paid at higher rate. Workers also get wages for idle time which helps to increase the cost of production per unit.
- Difficulty in preparing quotations – It is not possible to ascertain the exact labour cost per unit because it will change if output falls or rises. So difficulty is experienced in sending the quotations for tenders.
- Conflict – The system may cause conflict between the management and workers since management wants maximum output and workers want maximum wages. Such conflict may lead to serious confrontation between management and workers.
- Increased cost of supervision the system needs close supervision to ensure continuity of operations which results in increased cost of supervision.
There are a few variations of the time rate system with a view to introducing an element of incentive in the time wages. These methods are:
High Wage Rate:
Under this wage system, a time rate of a worker is fixed at a higher level than the average wage rate of the industry. The wage rate is fixed by hour or day. Higher rate is given to attract efficient workers. Overtime is not permitted under this system. Stable working conditions are created to enable the workers to achieve the standard output within the regular hours of work. Those who are not able to achieve the standard are taken off the scheme.
Graduated Time Rate:
Under this method, wages we paid at time rates which vary with changes in cost of living index. The wage rate per hour or per day goes on changing with changes in the general cost of living index. This system is preferred by the workers during the time of rising prices because their wages go on increasing with increase in the cost of living index. In India, the basic wage rates normally remain fixed and the worker is paid dearness allowance which rises with cost of living.
(c) Differential Time Rate:
Under this wage plan, different wage rates are fixed for different levels efficiency. Normal time rate is paid to the workers up to certain percentage efficiency. The rate gradually increases beyond the standard. Thus higher rates are giving to efficient workers in recognisation of their efficient performance.
PIECE RATE OR PIECE WAGE SYSTEM
This system is also known as payment by results. When wages are paid on that basis of the output of the workers without considering the- time taken in performing work, it is termed as piece wage.
Thus under this system, the workers are paid on basis of quantity of work done, i.e., per unit of output, per article, per job, commodity, etc. For computing total remuneration of workers, a pre-determined rate unit of output is multiplied by the total units produced. The rate is fixed with the of time and motion studies. The formula for wage computation under this system is:
Wages = Number of units produced x Rate of wage per unit
For example, a worker produces 8 units in one day and the rate of wages per unit is $ 10. The total wages for the day would be: 8 x $ 10 = $ 80
Suitability of Piece Rate System
Piece rate system of payment of wages is considered suitable:
- Where the quantity of work done can be precisely measured and standardized.
- Where the work is of repetitive nature.
- Where it is possible to fix a fair and acceptable piece rate.
- Where the productivity is closely related to skill and efforts.
- Where the quality of goods can be controlled.
- Where time cards are maintained for ensuring regularity and punctuality of workers and uninterrupted flow of production.
- Where materials, tools and machines are pettily available to cope with the possible increase in production.
Advantages
Important advantages of the piece rate system are:
- Fairness – Under this system, the reward is related to effort. Efficient workers are rewarded and inefficient workers are penalized.
- Increase in productivity – More work is turned out in a shorter period of time. Since there is a direct incentive to work, there is always a tendency on the part of the worker to produce more by adopting correct procedure and techniques of production.
- Decreased cost of production – Increase in production results in lower costs due to the reduction in fixed cost and overhead cost per unit of production.
- Easy determination of quotation price – The employer is able to know the exact labor cost per unit. This will help to make quotations confidently and accurately.
- Less Supervision – As compared with the time rate system, the supervision costs under this system are not high, because the workers are to be paid on the bases of performance. The very attraction of greater reward for greater effort drives them to work hard.
- Reduction of Idle time – The quantum of idle time is minimized as workers know that they will not be paid for idle time. Thus it persuades them not to waste their time.
- Minimization of loss due to breakage – The workers handle the machines, toes and implements with great care which helps in minimization of loss resulting from breakage. They know that the breakage will reduce their output which results in reduced wages.
Disadvantages
Some important disadvantages of the system are given below:
- Difficulty in fixation of standard piece rate – Setting of a standard rate involves a lot of difficulties and a considerable amount of expend’ has to be incurred. If high piece rate is established, it is very difficult reduce it subsequently.
- Ignores quality – As more output means more wages, the workers always in a hurry to produce more. This results in production of’ standard items, high rate of rejection and ultimately increased c, production per unit.
- Insecurity – The system does not provide guarantee of minimum of wages to the workers. They feel in secured since they would get wages during the period when their efficiency may get reduced factors beyond their control. Thus, at times, workers may be earning even below the subsistence level.
- Conflict – The system may lead to conflict between the managemen’1the workers, if the output is low due to some fault of the management, as, bad quality of raw material, frequent break-downs of machinery/ failure, etc.
- Expensive control systems – Management is compelled to intern expensive control systems of supervision and inspection for maintained of quality of output.
- Speeding – Workers may speed up the work to produce more which cause great injury to their health, speeding also causes undue wastage raw materials and very and tear to machines.
- Effect on production schedule – Workers may work at a seed for a day, earn more wages and then absent themselves for a few days, w may affect the uniform flow of production and the production such may be disturbed.
- Increased cost of production – Cost of production may increase due to more wastage of materials, high cost of supervision and inspection, and wear and tear of machines.
- Frustration among less efficient workers – The system will frustrate the less efficient workers and their efficiency may further decrease because of discontentment.
The piece rate system is of the following types:
(a) Straight Piece Rate:
This is the simplest and the most common type of piece rate system. Each operation, job or unit of production is termed as a piece. The wage rate fixed for each piece is called piece rate. The worker is paid wages on the basis of work done regardless of the time taken to perform the work. The wage of a worker is calculated by multiplying the number of units produced by him by the specified rate for each unit.
Wages = Number of units produced x Wage rate per unit
The piece rate is fixed with the help of work study. Standard time for each unit is ascertained first. Piece rate is then calculated with reference to hourly rate of wage. For example, if hourly rate of wage is $ 10 and the standard time per unit is 90 minutes,
(b) Piece Rate with Graduated Time Rate:
Under this system, workers are actually paid on the basis of output and if the piece rate wages fall below the time rate wages, the worker is paid on time rate basis.
The difference will be recovered from his wages when he earns more than the fixed wages. For example, in a manufacturing concern, the piece rate is $ 4 per unit, the time rate is $ 80 per day of 8 hours and the daily fixed work is 20 units.
If a worker manufactures 18 units in a day, the earns $ 72 ($ 4 x 18) on the basis of piece rate. But he will get $ 80 as his time wages which is $ 8 more than what he earns on piece rate basis and this amount of $ 8 paid to him in excess will be recovered from his wages whenever his piece rate wages exceed the time rate wages.
But if the word manufactures 22 units in a day, he will get $ 88 ($ 4 x 22) on piece rate basis. This system has all the merits of both the time and piece rate systems and removes demerits of both. But it is a very complicated and difficult system for the workers understand.
(c) Differential Piece Rate System
Under the differential piece rate system, the payment of wages is made to labor on the basis of piece rates varying with the level of efficiency of workers. The system provides for higher rewards to more efficient workers. Under this system, there is more than are piece rate to reward efficient workers and to encourage the less efficient workers to improve. Payment at normal piece rate is made for work performed with and up to the standard level of efficiency. Payment is made at higher piece rate if the efficiency exceeds the standard. Higher piece rates are also applicable for still high efficiency. The system motivates the workers to increase productivity and earn higher wages. The system is complicated and expensive to operate and is difficult for the workers to understand.
I have not checked in here for a while as I thought it was getting boring, but the last several posts are great quality so I guess I will add you back to my daily bloglist. You deserve it my friend 🙂
Somebody necessarily help to make severely posts I’d state. This is the first time I frequented your web page and so far? I surprised with the research you made to make this particular publish amazing. Excellent job!
The articles you write help me a lot and I like the topic
Hello there, I found your site via Google while searching for a related topic, your website came up, it looks good. I’ve bookmarked it in my google bookmarks.
I’m so in love with this. You did a great job!!
Well I truly liked reading it. This post procured by you is very useful for good planning.